Es garantiert ein Höchstmaß an Präzision für die verschiedenen genormten Probenformate.
Ebenso erledigen wir für unsere Kunden Zuschnittarbeiten verschiedenster Materialien und Formate.
Beim Hochdruckwasserstrahlschneiden wird ein Wasserstrahl mit einem Druck bis ca. 4000 bar und einer Austrittsgeschwindigkeit von knapp 1000 m/s eingesetzt.
Es gibt 2 Varianten:
- das Reinwasserschneiden ohne Zusätze im Schneidstrahl und
- das Abrasivschneiden unter Beimengung von Abrasivmaterial (Granatsand) im Schneidstrahl.
Reinwasseranwendungen eignen sich im Besonderen zum Schneiden von Papier, Kunststoffen, Schaumstoffen, Textilien, Leder, Dichtungsmaterial, Silikon, Lebensmitteln und Holz.
Typische Anwendungen für Abrasivschneidprozesse sind Materialien wie Stahl, Aluminium, Titan, Kupfer, Messing, Bronze; Keramik, Glas und Gestein. Es ist ebenfalls möglich Kompositwerkstoffe zu trennen sowie sehr dünne (0,5 mm) bis sehr dicke (200 mm) Werkstoffe zu schneiden. Es gibt kaum Einschränkungen bezüglich der Schneidbarkeit der unterschiedlichen Materialien oder Materialkombinationen.
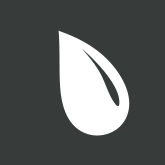
Vorteile
Der wesentlichste Vorteil des Wasserstrahlschneidens ist, dass durch den eigentlichen Schneidprozess keine thermischen Einflüsse auf das zu schneidende Material einwirken. Gefügeveränderungen an den Schnittflächen oder den benachbarten Zonen, ebenso Verwerfungen, Maßabweichungen bzgl. der Ausdehnung durch Wärmeeintrag sind nicht gegeben.
Bei Verwendung entsprechender Schneidparameter kann der Zuschnitt so erfolgen, dass ein mechanisches Nachbearbeiten entfällt. Die Fertigteilerzeugung ist bei angepassten Vorschubgeschwindigkeiten optimal umsetzbar. Komplexe Geometrien und Konturen lassen sich durch den Betrieb im 2D- und 3D-Modus, durch Übernahme aller gängigen CAD-Daten (DXF, DWG…) vom Einzelteil bis zum Serienteil kostengünstig realisieren.
Bei geringen Schnittfugenbreiten können kleinste Radien erzeugt werden. Eine maximale Materialausnutzung mit einer hohen Verschachtelungsdichte ist das Ziel. Die Bauteile lassen sich mit Gravuren für Zeichnungsnummern, Positionen, Anrissen und Körnern für nachfolgende Bearbeitungsschritte kennzeichnen.
Ein Nachschärfen von Werkzeugen, wie es bei konventionellen Bearbeitungsmethoden (Sägen, Fräsen) notwendig ist, entfällt. Umweltbelastungen durch Rauche oder Dämpfe aus dem Schneidprozess sind prinzipiell ausgeschlossen, da nur reines Wasser und Granatsand verwendet werden.